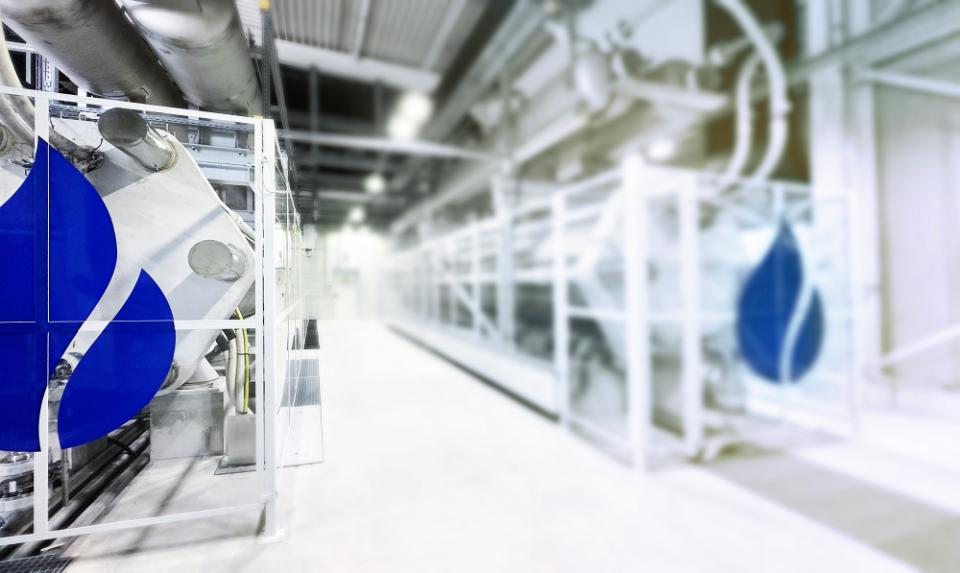
News
KK Wind Solutions to deliver largest Power Supply Unit to date
The company will deliver a 100 MW Power Supply Unit to leading electrolysis specialist Sunfire.
Press contacts is for media enquiries only.
For general requests please contact our main reception desk, and they will forward you to a relevant person.
We strive to answer as fast as possible.
Explore how we create value for our customers and access expert insights.